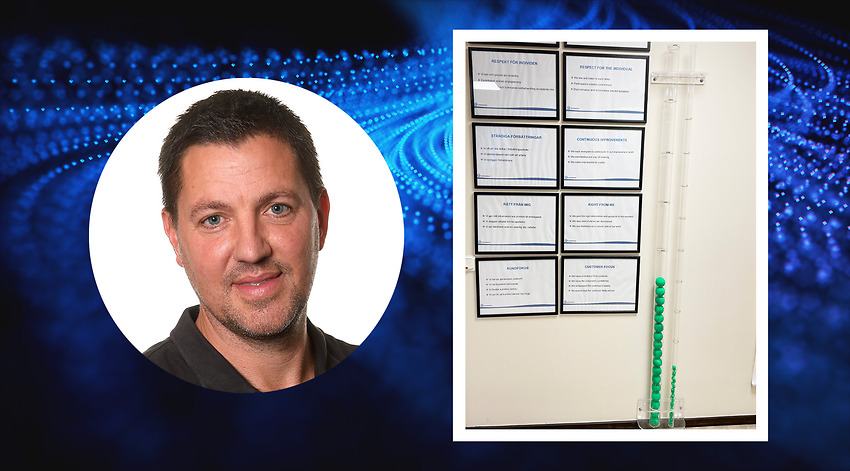
It has been almost 10 years since Elektromontage introduced the LEAN model led by Tobias Lindén. The model includes improvement work, which we have been good at. All employees have set aside an hour a week to work in groups to reduce waste and to improve quality and safety based on the focus on increasing profitability while maintaining a good working environment. So far, we have implemented more than 1,700 improvements, we have 70 projects in progress and 100 proposals that are waiting to be assessed and dealt with.
The first thing visitors meet in our reception are two transparent tubes with cotton pulp balls. A tube where we add a green ball for each implemented improvement and a tube with larger balls each of which symbolises hundreds of improvements. The attentive can see that as of today we have implemented 1,722 improvements.
– Many of our visitors think it is fun to see it so visual,” says Tobias Lindén, site manager at Elektromontage.
He introduced the LEAN model to the company just over ten years ago, where one of the cornerstones is to work on improvements.
– We are starting from a standard, a situation that is constantly improving. The work also involves developing standards for how activities and work tasks are to be carried out so that we do not depend on the knowledge of individual employees. This makes the company more robust and also provides a mechanism for learning new things.
Planning, prioritisation and implementation
Employees are divided into nine different improvement groups and spend one hour per week planning, prioritising and implementing improvements.
– Every month we summarise how many improvements have been made and how many new ideas have emerged. When we reach a hundred improvements, we celebrate with Swedish Smörgåstårta or something else that is appreciated.
All ideas are evaluated on how much effect they have and how easy they are to implement. The groups then prioritise which improvement proposals they should work with.
– Right now we have focused on improvements that primarily increase profitability without restricting the working environment.
Tobias says that we have, for example, made a tool for mounting hard-to-reach screw joints.
– It has made the work both more efficient and safer for the hands.
In addition, we have recently arranged a mobile cable stand that saves a lot of unnecessary running and we have prepared a customer solution for cooling cabinets with pneumatics that are in an ambient temperature of more than 50 degrees.
Tobias finds it fascinating that the improvement work is working so well and that everyone at the company is involved.
– The fact that employees have the opportunity to participate and influence their work is appreciated and we almost never say no to ideas that are put forward. Our improvement work creates participation and makes Elektromontage more competitive as a company.